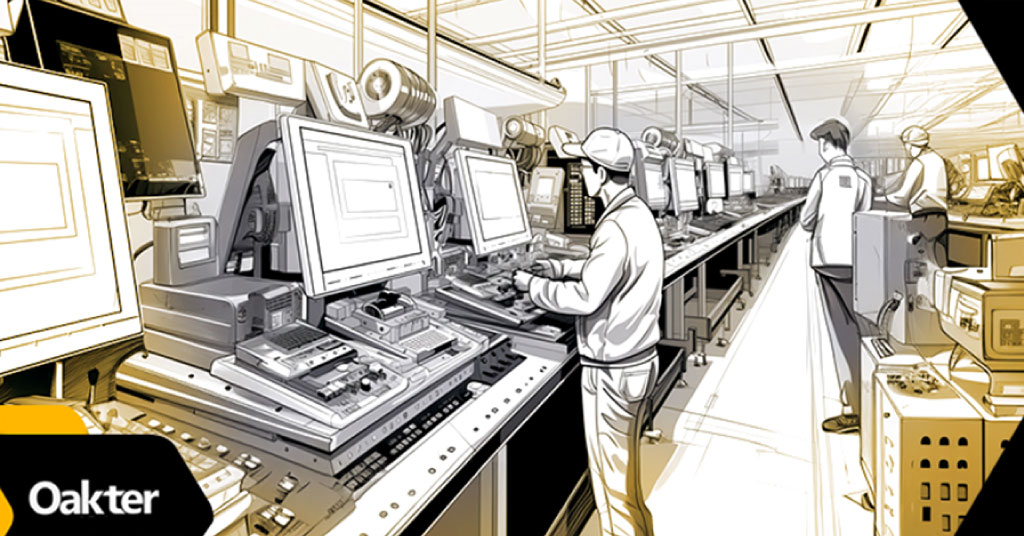
Breaking Down Costs: A Comparative Analysis of Contract Manufacturing vs. Traditional Manufacturing
The manufacturing industry is the backbone of global economies, driving innovation, employment, and economic growth. It encompasses many sectors, from automotive and electronics to pharmaceuticals and consumer goods.
Manufacturers also play a vital role in transforming raw materials into finished products, employing various production methods and technologies.
Therefore, understanding and comparing costs in the manufacturing industry is essential for businesses to remain competitive. Costs can significantly impact profitability, pricing strategies, and overall business success.
Efficient cost management allows companies to allocate resources effectively and make informed decisions about production processes. In fact, studies show that efficient cost management can increase profitability by 10-15%.
In this article, we delve into the realm of contract manufacturing as an alternative approach to traditional manufacturing.
What is Traditional Manufacturing?
Traditional manufacturing, also known as in-house manufacturing, refers to the conventional approach where companies handle all aspects of production internally. It involves the entire production process, from designing and sourcing materials to assembling and distributing the final product.
In traditional manufacturing, companies maintain control over every stage of production. This allows for customisation, quality assurance, and protection of intellectual property.
However, it comes with certain challenges. One major disadvantage is the need for substantial upfront investments in facilities, equipment, and skilled labour.
Types of Traditional Manufacturing
Traditional manufacturing can be classified into different types based on the production method employed:
1. Repetitive manufacturing
This type involves the production of identical or highly similar products in large quantities, often using assembly line techniques.
2. Discrete manufacturing
Discrete manufacturing focuses on producing individual, distinct items, such as automobiles or appliances, with unique specifications and features.
3. Job shop manufacturing
Job shop manufacturing caters to customised and low-volume production. It involves the production of products tailored to specific customer requirements.
4. Continuous process manufacturing
Continuous process manufacturing is used for producing goods with continuous or uninterrupted flow, such as chemicals or petroleum products.
5. Batch process manufacturing
Batch process manufacturing involves producing goods in batches or specific quantities, typically for a limited period. It allows for flexibility in adjusting production levels and enables easier quality control.
Contract Manufacturing: An Alternative to Traditional Manufacturing?
Contract manufacturing has emerged as a strategic approach for businesses looking to streamline their production processes and optimise costs. But what exactly is contract manufacturing?
Contract manufacturing refers to the outsourcing of production processes to specialised manufacturers, known as contract manufacturers. Under this arrangement, a company entrusts the manufacturing of its products to a third-party while retaining control over design, branding, and distribution.
The advantages of contract manufacturing are significant. It offers cost savings through economies of scale and supply chain networks while providing expertise and advanced technologies to enhance product quality and efficiency.
Here are the different types of contract manufacturing agreements that we will be discussing next:
1. Original Equipment Manufacturing (OEM)
The contract manufacturer produces goods based on the hiring company’s specifications and design in this agreement. The hiring company provides the required components and intellectual property, while the contract manufacturer handles the production and assembly.
2. Original Design Manufacturing (ODM)
In the ODM agreement, the contract manufacturer produces the goods and assists in the design and development process. The hiring company provides basic specifications, and the contract manufacturer takes responsibility for the detailed design, manufacturing, and sometimes branding.
3. Electronics Manufacturing Services (EMS)
EMS refers to a specialised type of contract manufacturing focused on electronics. Contract manufacturers offering EMS take charge of manufacturing electronic components or complete electronic products based on the hiring company’s requirements.
Comparative Analysis of Costs: Contract Manufacturing vs. Traditional Manufacturing
When it comes to manufacturing, understanding and comparing costs is vital for businesses to make informed decisions. Let’s explore key factors that impact the bottom line.
1. Labour Costs
Labour costs play a significant role in manufacturing expenses. Contract manufacturing often offers cost advantages as it allows businesses to tap into regions with lower wages and benefits.
Traditional manufacturing, on the other hand, may face higher labour costs due to factors like local market conditions and labour shortages.
2. Overhead Costs
Overhead costs encompass facility expenses, utilities, and maintenance. Contract manufacturing can help reduce overhead costs since the onus falls on the contract manufacturer. In traditional manufacturing, companies must invest in their facilities and bear expenses like rent, utilities, and ongoing maintenance.
3. Material Costs
Material costs are a critical component of manufacturing expenses. Contract manufacturers often have established procurement channels, enabling them to source materials at competitive prices.
They can leverage bulk purchasing and economies of scale to achieve cost savings. Traditional manufacturers may face challenges in sourcing materials efficiently, potentially leading to higher costs.
4. Equipment and Machinery Costs
Investment in equipment and machinery is a significant consideration for manufacturers. In traditional manufacturing, companies bear the capital investment and depreciation costs of acquiring and maintaining equipment.
Contract manufacturers, on the other hand, take responsibility for equipment and machinery costs, alleviating the financial burden on the hiring company.
5. Quality Control and Assurance Costs
Ensuring product quality is crucial for manufacturers. Traditional manufacturers have direct control over their quality control processes, which comes with associated costs.
Contract manufacturers often specialise in quality control and have established systems in place. While outsourcing quality control can reduce costs, it’s essential to carefully evaluate potential risks and consider the impact on overall quality.
6. Regulatory Compliance Costs
Regulatory compliance is a key consideration in manufacturing. Compliance requirements may vary depending on the industry and product, impacting manufacturing processes and associated expenses.
Contract and traditional manufacturing need to navigate these compliance obligations, which can influence overall costs.
Which service is best for you- Traditional Manufacturing or Contract Manufacturing?
The decision between traditional manufacturing and contract manufacturing depends on various factors, including your business objectives, product complexity, production volume, and budget.
Traditional manufacturing offers control and customisation but requires substantial investments and may lack scalability. On the other hand, contract manufacturing offers cost savings, access to expertise, and flexibility, but it involves relinquishing some control over the production process.
Consider the advantages and disadvantages of each approach, and weigh them against your specific needs and goals. Ultimately, the right choice will depend on your unique business circumstances.
Making Informed Decisions for Manufacturing Success
As you evaluate manufacturing options for your business, carefully consider the costs associated with traditional manufacturing and contract manufacturing. Assess the specific needs of your product, industry, and business goals.
The future of manufacturing lies in optimising costs while maintaining quality, and contract manufacturing can play a vital role in achieving that. So, take the time to make an informed decision and explore the possibilities contract manufacturing can offer.
If you need manufacturing assistance, choose Oakter as your trusted partner. We are an Advanced Indian ODM facilitating concepts to large-scale manufacturing processes.
To discover how our services can propel your business forward in the ever-evolving manufacturing industry, contact us today!