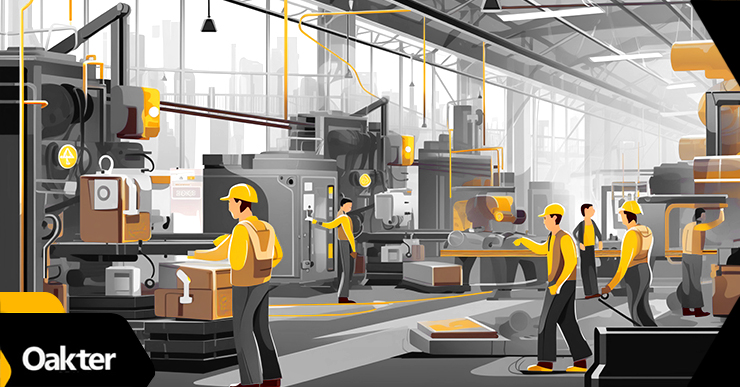
The Basics of Box Build Manufacturing: A Comprehensive Guide
For electronic manufacturers, the one-size-fits-all approach is becoming outdated. Not all projects are cut from the same cloth, and assembly methods shouldn’t pretend they are. Thankfully, there’s the box build manufacturing.
Consider this: Doesn’t your unique project deserve a custom assembly process? With the advent of box build manufacturing, you have a path to holistic systems integration. So the question is, why opt for standard assembly and miss out on a targeted solution for full-scale systems integration?
In this blog, we will explore the substantial difference box build manufacturing brings to your projects.
Box Build Manufacturing: An Overview
Box build manufacturing, commonly known as “systems integration,” involves assembling different electronic and mechanical parts to create a complete product. Although this isn’t just any assembly process, it’s tailored to meet the specific needs of each unique project.
This might be as straightforward as putting together a circuit board enclosure or as complex as setting up a large telecom system. The process encompasses connecting wires, mounting components, and securely housing electronics. However, when we refer to box build manufacturing, it’s an advanced approach in this domain, emphasising the distinct requirements of every electronic endeavour.
Components of Box Build Manufacturing
Each component plays a pivotal role in achieving an efficiently assembled electronic product for box build manufacturing. These include:
1. Enclosures
Acting as the protective shield, these can be crafted from metals, plastics, or hybrid materials, encapsulating the sensitive internal components.
2. Wiring and Harnesses
The veins of the assembly connect various components within the enclosure, ensuring seamless communication.
3. PCB Assemblies
Often considered the heartbeat of box build manufacturing, these pre-assembled boards carry the electronic components that make the system come alive.
4. Sub-assemblies
These smaller units are integrated into the larger system, working harmoniously with other components.
5. Interface Panels
Not just about inner workings, box build manufacturing also emphasises user interaction and connectivity achieved through these panels.
6. Testing Equipment
Vital to the integrity of the end product, these tools ensure that the final assembly functions precisely as envisioned.
The Box Build Manufacturing Process
At its core, the box-build process is as diverse as the spectrum of designs it caters to—unique to every project and meticulously curated to meet distinct requirements. Though bespoke in nature, the process generally includes a series of quintessential steps:
- Installation of Sub-Assemblies and Components: This foundational phase sees various components paving the way for a robust electromechanical system outfitted with moving parts and sub-assemblies.
- Routing and Cabling: Ensuring seamless communication and function, wire harnesses and cables are adeptly routed.
- Enclosure Fabrication: A protective casing or enclosure is crafted, ensuring the assembled unit remains safeguarded.
- Configuration and Testing: A critical phase, ensuring the assembly performs optimally, resonating with the design’s intent.
- Warehousing and Shipping: The final touchpoint, where the assembled product is stored and then dispatched, making its way to its intended destination.
4 Key Considerations in Box Build Manufacturing
Venturing into box build manufacturing necessitates a nuanced approach. It intertwines intricate processes, diverse components, and unique project demands.
Let’s delve into the pivotal factors that underpin the success of this intricate manufacturing endeavour.
1. Flexibility
Box build manufacturing projects are as diverse as they come. Whether it’s a change in the assembly process or a variation in component sourcing, a successful box build manufacturing setup can adapt on-the-fly.
Given the unpredictable nature of custom electronic projects, the ability to pivot without compromising the timeline or quality becomes an invaluable asset. This operational agility ensures the project remains on track even when the client requirements scale.
2. Quality Control
At the core of any manufacturing venture lies the uncompromised quality of the end product. In box build manufacturing, this means rigorous testing at every phase and meticulous assembly inspection. The end goal? A product that isn’t just reliable and stands the test of time.
3. Scalability
In a dynamic market, fluctuations in demand are commonplace. The prowess of a box build manufacturing setup is often gauged by its ability to scale operations seamlessly. Whether it’s a surge in demand or a need for limited prototypes, being equipped to handle varied production volumes is paramount.
4. Customisation
Every project presents unique challenges and specifications. This is where the capability of box build manufacturing comes into play. It can help you tailor and customise your processes to make the end products indispensable. The more customised the approach, the more aligned the end product will be with client expectations.
Challenges in Box Build Manufacturing
As with any intricate process, box build manufacturing comes with its hurdles. Here are the multifaceted challenges that manufacturers often grapple with in this domain:
1. The Complexity of Modern Components
As tech keeps evolving, our gadgets and devices become much more complex. Think about it: one device can have a ton of tiny parts all working together. This escalating complexity demands higher expertise, precision, and understanding of the nuances involved.
2. Consistent Supply of Top-Tier Components
The success of a box build manufacturing project often hinges on the timely and consistent supply of quality components. Any disruption in the supply chain, be it due to geopolitical reasons, logistics, or supplier inconsistencies, can throw a wrench in the works, potentially delaying projects and escalating costs.
3. Balancing Premium Quality with Financial Prudence
The financial tightrope in box build manufacturing is a challenging one to tread. On one side lies the imperative to source top-notch components; on the other, the pressing need to keep overheads in check. Striking a balance, where quality doesn’t get sacrificed at the altar of cost-cutting, demands sharp financial acumen.
4. Staying Ahead in the Regulatory Compliance Race
More than most, the electronics sector is bound by a web of regulations and standards. These ensure product safety, quality, and eco-compatibility. Navigating this regulatory compliance while ensuring that the product remains cutting-edge adds another challenge to the box build manufacturing process. However, partnering with the right firm can solve this for you.
Embracing the Future of Your Box Build Manufacturing With Oakter
Box build manufacturing offers specialised assembly processes that celebrate the uniqueness of every project. Yet, it’s not without challenges. This makes it crucial for manufacturers to find the right partner.
If you’re looking for a partner in this journey, Oakter stands tall as a reliable partner. We are the champions of the cause of innovative electronic manufacturing.
Moreover, Oakter is not just any Original Design Manufacturer. We offer a confluence of thought, innovation, and commitment. Shipping over 500k products a month, with deep insights into IoT, Oakter is well-equipped to transform concepts into large-scale manufacturing realities.
Aligning with a partner like Oakter ensures you’re not just keeping pace but leading the charge.