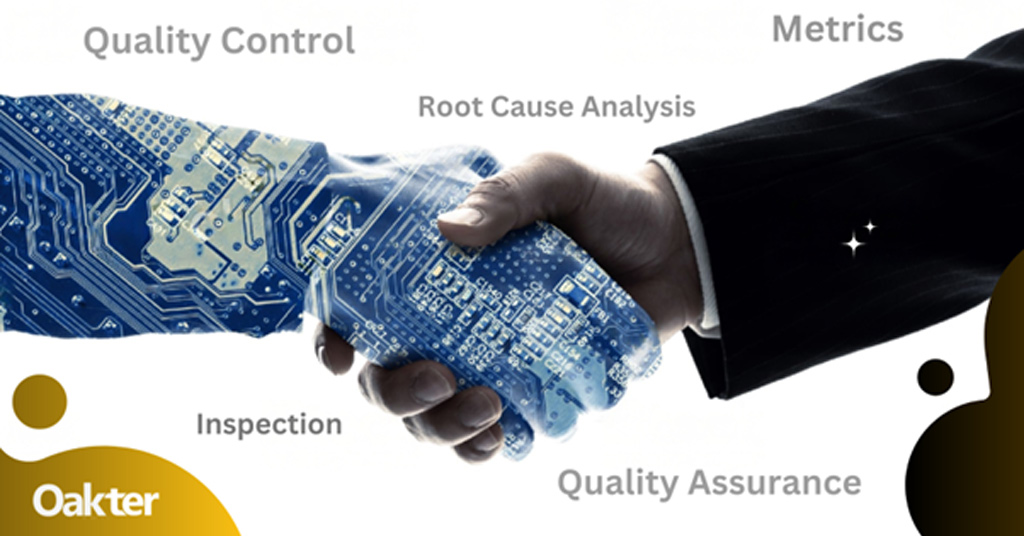
Partnering for Quality: A Guide to Success in Contract Manufacturing
Are you ready to outsource the production of your products to a contract manufacturer?
Considering several aspects, contract manufacturing is a smart move that allows you to focus on other aspects of your business, but it’s crucial to maintain quality control throughout the process. After all, the contract manufacturer is essentially an extension of your brand, implying you want the final products to reflect your company’s values and standards.
This blog post will explore the secrets for ensuring quality in the contract manufacturing process: from setting clear expectations to implementing ongoing quality control measures.
5 Things To Ensure Before Partnering With A Contract Manufacturing Company
Follow these tips to ensure that your contract manufacturing partnership succeeds and that the final products meet your high standards.
1. Establish Clear Expectations
Before you partner with a contract manufacturing partner, get a clear understanding of what you expect from the relationship. This includes setting clear standards for quality, delivery times, and communication.
It’s important to be specific about what you expect from the final products to ensure that you meet the quality standards. It includes setting standards for materials, dimensions, and performance. Also, you may provide examples or prototypes of what you envision as the final products.
Secondly, be realistic and consistent about your deadlines and provide an adequate lead time for the contract manufacturing partner to complete the work. It can also be helpful to build in some flexibility in case of unexpected delays or issues.
Remember, effective communication is key to any successful partnership. Ensure that you establish clear communication channels with your contract manufacturing partner and set expectations for how and when you will communicate with each other. This can include regular meetings, updates, and project management tools to track progress.
Finally, outline all these expectations in a written agreement so that everyone is on the same page and there are little to no misunderstandings.
2. Conducting Thorough Evaluations of Potential Manufacturers
It’s essential to do your due diligence when selecting a contract manufacturing partner. This includes evaluating their facilities, processes, and quality control measures to ensure they meet your standards. You should also consider their experience and reputation in the industry and ability to scale production as needed. It is recommended that you commit to a few things before finalising the deal:
- Research the manufacturer’s reputation
- Review their facilities and processes
- Request samples
- Evaluate the manufacturer’s communication and responsiveness
- Discuss quality control measures
3. Implementing steady quality control measures
Quality control continues even after production begins because you must have ongoing measures to ensure that the final products meet your standards. This can include regular inspections, testing, and communication with the contract manufacturing partner to address potential issues.
Conduct periodic inspections of the contract manufacturer’s facilities and processes and ensure that the products are being produced to your standards. For example, conduct visual inspections, testing of materials, or other methods to assess the quality of the products.
Test your final products to identify any issues or defects before delivering them to end customers. This might include functional testing, durability testing, or other tests relevant to your products.
Maintain open communication with the contract manufacturing partner to reduce issues during production. Discuss any concerns you have about the quality of the products, or provide feedback to the manufacturer on ways to improve the process.
4. Establish a Strong Relationship With Your Contract Manufacturers
Build a positive relationship with your contract manufacturing partners to ensure the partnership’s success and the quality of the final products. Foster trust and be transparent and flexible with your contract manufacturing partners. Being open to modifying the production process or adjusting deadlines as needed always helps.
Maintain a schedule of regular meetings to address unforeseen issues promptly. It could be weekly or monthly check-ins and ad-hoc meetings as needed. You can also leverage project management tools like Trello or Asana to keep track of progress.
Also, provide genuine feedback to your contract manufacturing partner. It’ll help them understand what you expect from the final products and how they can improve the process. Practice constructive criticism of any issues you’ve identified, and suggest how to improve the quality of the products.
5. Contingency Plan
Things don’t always go as planned. Therefore you should have a contingency plan in case of unexpected issues. This includes having backup suppliers or the ability to shift production to another manufacturer if necessary.
Here are a few different things you can incorporate into your contingency plan:
- Alternative suppliers: It’s a good idea to have a list of backup suppliers for critical materials or components in case of shortages or disruptions.
- Alternative manufacturing options: If you cannot work with your current contract manufacturing partners, it’s crucial to have a plan to shift production to another manufacturer. This might include having a list of potential manufacturers to contact in an emergency and a method for transitioning production to a new manufacturer.
- Contingency budget: It’s a good idea to set aside a contingency budget to cover unexpected costs, such as costs associated with finding a new supplier or manufacturer or expenses related to delays or disruptions in production.
Final Thoughts
In today’s fast-paced business world, outsourcing production to a contract manufacturer can be a smart way to focus on other areas of your business. But it’s crucial to ensure that the quality of the final products meets your standards. By following the best practices mentioned above, you can safeguard the quality of your products and your brand’s reputation. Take advantage of these crucial steps – a little bit of effort upfront can go a long way in preserving the integrity of your brand and keeping your customers happy.
Oakter can help you achieve this. We are an ODM manufacturing organisation dedicated to delivering quality products at affordable rates. Besides maintaining a track record of shipping 500k+ made-in-India products per month, our ever-expanding portfolio includes developing quality products and white-label solutions for our exclusive partners.
Reach out to us today!