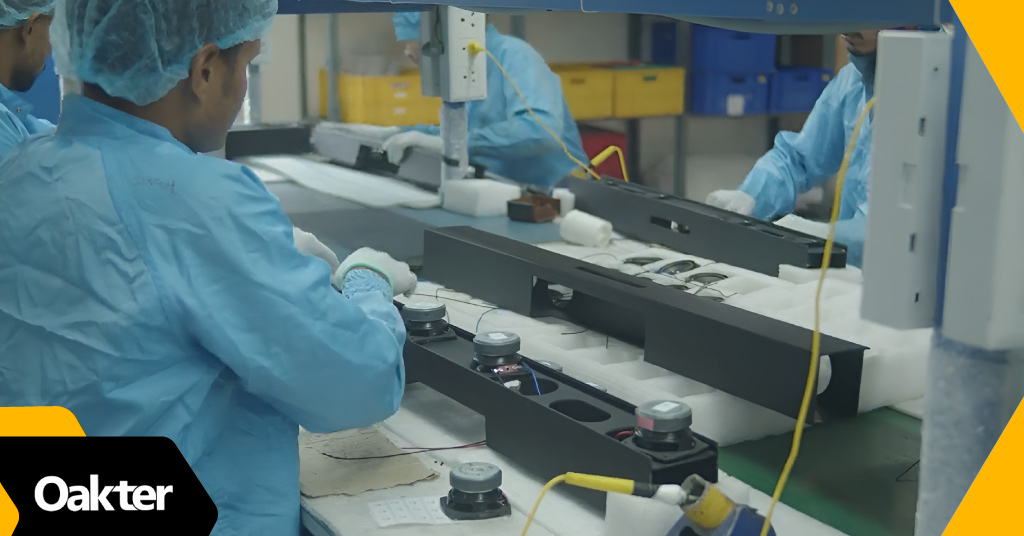
Understanding the Complete Process of Sound Bar Manufacturing
Sound bars have significantly altered home entertainment. These compact devices fit just under your TV and provide surround sound without the effort of setting up numerous speakers.
Despite their straightforward appearance, creating a sound bar is a complicated process. To achieve the ideal sound, various engineering and testing processes must be conducted as part of a labourious manufacturing process incorporating innovative technology, precise engineering, and stringent quality control.
In this article, we will delve into the complete process of sound bar manufacturing, from the initial design stages to the final quality control checks.
What Is a Sound Bar?
Soundbars are speakers designed to project sound across a large area. They are not particularly tall but quite lengthy. Due to their slender design, They can be mounted atop a TV or PC, or you can use them as an auxiliary to a home theatre system.
The most notable feature of this device is its superior sound quality, smaller speakers or speakers built into gadgets. Soundbars eliminated the need for people to choose between poor audio quality and exorbitant surround sound costs by providing better audio without being as expensive.
Also, they are quite easy to install with simple plug-and-play and Bluetooth features.
The Sound Bar Manufacturing Process
In this section, let’s explore the entire process of sound bar manufacturing, from the initial design stages to the final quality control checks.
1. Conceptualisation and Design:
Designing and conceptualising are the first steps in the sound bar manufacturing process. Market research, evaluating consumer preferences, and selecting the target market are all part of this step. Engineers and designers work together to develop a great product that looks attractive and fits seamlessly into home environments.
Key steps in this stage involve:
- Market Research: This identifies consumer preferences and market trends to ensure the product fits the market’s needs and expectations.
- Design Development: This is the process of creating intricate product designs, complete with specifications for the product’s size, shape, materials, and components.
- Acoustic Engineering: It involves designing the sound bar’s audio parts, such as the speakers, amplifiers, and signal processing, to achieve optimal sound quality.
2. Material Selection
After the design is complete, the next step is choosing the materials used during the sound bar manufacturing. To achieve aesthetic and sonic objectives, sound bars frequently combine materials like plastics, metals, and different speaker cones.
Materials selection includes considerations such as:
- Durability: Ensuring the materials are strong enough to resist the manufacturing process and normal wear and tear.
- Aesthetics: Choosing components that improve the design of the sound bar, such as brushed aluminium, for an elegant appearance.
- Acoustic Properties: Choosing materials with the right acoustic properties, such as resonance-absorbing ones that dampen vibrations, can help achieve the desired audio performance.
3. Manufacturing Process
Sound bar manufacturing involves a well-planned succession of complex processes, each of which is essential to creating these auditory miracles. Here are the key phases that make up this manufacturing process:
- Injection Moulding: The outer casing of the sound bar will be made using the injection moulding technique, which involves melting plastic and moulding it into the required shape.
- Electronics Assembly: This is the process of inserting electronic parts into a casing, such as speakers, amplifiers, circuit boards, and connectors.
- Wiring: Carefully connect all the internal components using precise wiring techniques to ensure proper functionality.
- Quality Control: Conducting quality checks at various stages of production to identify and address any flaws or problems
4. Speaker Integration
A sound bar’s speakers are among its most important parts. The speakers are precisely integrated into the casing to achieve optimal audio quality. This entails:
- Speaker Placement: Carefully positioning the speakers within the sound bar to ensure balanced sound distribution and minimize interference.
- Acoustic Tuning: The desired sound profile, including bass response and clarity, is achieved by fine-tuning speaker placement and internal architecture.
- Testing: Conducting audio tests to ensure the speakers produce high-quality sound and meet the specified performance standards
5. Connectivity and Electronics
Sound bars often come equipped with various electronic features and connectivity options. This stage of sound bar manufacturing entails:
- Amplifier Installation: Including amplifiers to power speakers and control volume.
- Ports for Connectivity: Including ports for Bluetooth, Wi-Fi, HDMI, and other connectivity options.
- Signal Processing: Implementing signal processing algorithms to improve audio quality through the use of equalisation and virtual surround sound, for example.
6. Shipping and Packaging
The sound bars are prepared for packaging once they have passed all quality control inspections. This entails:
- Packaging Design: Design packaging to protect the sound bars during shipment and exhibit them to customers in an appealing manner.
- Labelling: Including labels with brand names, specifications, and product information.
- Distribution: Sending the packed sound bars to retailers or selling them to customers online.
Key Takeaway
Sound bar manufacturing is intricate and highly specialised, with several steps from conception and design to quality assurance and shipping. Manufacturers work hard to offer products that provide excellent audio quality and meet customers’ expectations for aesthetics and functionality.
By understanding this comprehensive process, customers can appreciate the engineering and workmanship that go into manufacturing these essential components of modern home entertainment systems.
Outsourcing soundbar manufacturing is a practical decision for companies aiming to reduce costs and improve efficiency. Collaborating with electronic contract manufacturers enables access to specialised expertise and advanced production facilities, resulting in high-quality soundbars that align with market demands.
This approach allows businesses to concentrate on innovation, marketing, and customer service while entrusting the intricate manufacturing process to experienced professionals.
Oakter, a prominent electronic contract manufacturer headquartered in India, boasts a monthly shipment of over 500,000 products. Partnering with Oakter grants you access to the profound knowledge of manufacturing specialists, cost-efficient production, and top-notch products for your customer base.
One standout achievement in Oakter’s portfolio is the Saregama Carvaan Karaoke Soundbar, an innovative and unique product. Oakter took the lead in the development and design of this preloaded audio player, which has garnered widespread popularity in the market.
To know more, contact our team at Oakter today!