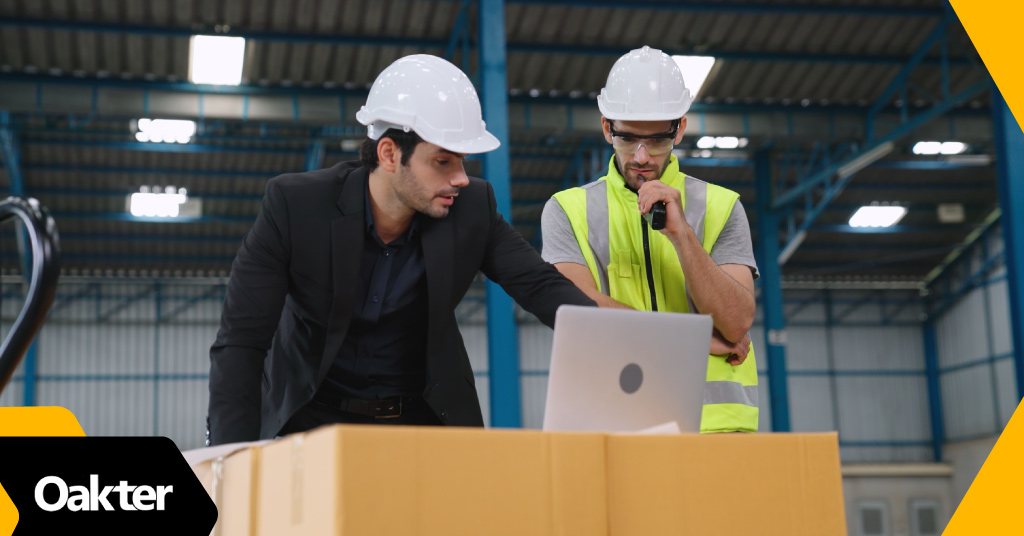
Reducing Lead Times: Strategies for Faster Turnaround with Outsourced Manufacturing Services
Outsourced manufacturing services are a form of business process outsourcing (BPO) that involves contracting with a third-party provider to produce goods or components.
Outsourcing can offer many benefits for businesses, such as lower costs, higher quality, and access to specialised skills and technologies.
However, outsourcing also comes with challenges, especially when managing lead times. Long lead times can result in higher inventory costs, lower flexibility, and lost sales opportunities.
According to a survey by Aptean, 88% of North American manufacturers are still experiencing longer-than-usual lead times due to supply chain disruptions.
Therefore, reducing lead times is a key objective for businesses that use outsourced manufacturing services. In this article, we will explore lead times, what factors affect them, and what strategies can help reduce them.
Understanding the Importance of Lead Times
Before we delve into the strategies to reduce lead times, let’s first understand what we’re dealing with.
What are Lead Times?
Lead times are the total time required to complete a production process, from when an order is placed to when the product is delivered to the customer. It can be divided into different types, depending on the stage of the production process.
What are the Different Types of Lead Times?
Some of the common types of lead times are:
- Procurement lead time: the time needed to obtain raw materials, parts, or components from suppliers.
- Production lead time: the time needed to transform the inputs into finished products.
- Delivery lead time: the time needed to transport the products from the manufacturer to the customer.
Key Strategies for Reducing Lead Times With Outsourced Manufacturing Services
Now, let’s explore some practical strategies to reduce lead times in outsourced manufacturing services:
1. Supplier Selection and Relationship Management
In the world of outsourced manufacturing services, selecting the right manufacturing partner is the cornerstone of reducing lead times.
a. Criteria for Selecting the Right Manufacturing Partner
When choosing an outsourcing partner, a thorough evaluation is necessary to ensure compatibility and reliability. Key criteria for selecting a suitable supplier should include:
- Assess the supplier’s production capabilities and capacity to meet your demand.
- Verify that the supplier meets stringent quality control standards and certifications.
- Seek clear commitments regarding lead times. The supplier’s historical performance in meeting lead time promises strongly indicates their reliability.
- Consider the supplier’s location concerning your business.
b. Building Strong Relationships with Suppliers
Once a manufacturing partner is selected, the journey toward lead time reduction continues with the development of solid and enduring relationships. Building these connections fosters collaboration and trust, smoother operations and reduced lead times.
2. Improved Communication
Improved communication is a pivotal strategy for reducing lead times in outsourced manufacturing services. To achieve this:
a. Real-time Communication Tools
Modern communication platforms and tools ensure swift and effective exchange of information between partners, helping to eliminate delays and misunderstandings.
b. Clear and Concise Specifications
Precise product specifications reduce the chances of errors and rework, streamlining the production process and expediting deliveries.
c. Regular Progress Updates
Implement regular progress updates to maintain transparency and accountability. These updates enable stakeholders to monitor project advancements, identify potential bottlenecks, and make necessary adjustments promptly.
3. Streamlined Production Processes
Streamlining production processes is a cornerstone of efficient manufacturing. It involves embracing lean manufacturing principles and fostering a culture of continuous process improvement.
a. Lean Manufacturing Principles
Lean principles aim to eliminate waste, reduce unnecessary steps, and optimise resource utilisation throughout the production cycle. By minimising non-value-added activities and focusing on value creation, businesses can significantly reduce lead times, enhance product quality, and lower production costs.
b. Continuous Process Improvement
To stay competitive, companies must commit to continuous improvement. This involves regularly evaluating existing processes, identifying bottlenecks or inefficiencies, and implementing changes to enhance productivity and reduce lead times.
4. Inventory Optimisation
This involves fine-tuning stock levels to strike a delicate balance between ensuring product availability and minimising carrying costs. This optimisation includes:
a. Safety Stock Management
Safety stock is a buffer of extra inventory that accounts for unexpected fluctuations in demand or supply chain disruptions. By carefully managing safety stock levels, businesses can mitigate the risk of stockouts while avoiding excessive holding costs.
b. Just-in-Time Inventory Practices
Just-in-time (JIT) inventory is a lean approach that aims to have inventory arrive precisely when needed for production or customer orders, minimising excess stock on hand. JIT practices streamline operations, reduce storage costs, and enhance efficiency by eliminating unnecessary inventory.
5. Technology Integration
Technology integration is pivotal in reducing lead times within outsourced manufacturing services.
a. Supply Chain Management Software
This software offers real-time visibility into inventory, orders, and production processes. It enables efficient resource allocation, demand forecasting, and order tracking, ultimately expediting lead times.
b. Internet of Things (IoT) for Tracking and Monitoring
Through IoT, tracking and monitoring become more accurate and responsive. This data-driven approach enhances decision-making, reduces delays, and contributes significantly to faster turnaround times in outsourced manufacturing services.
What are the Challenges and Considerations in Lead Time Reduction?
While reducing lead time can offer many benefits for businesses using outsourced manufacturing services, it can also pose some challenges and considerations, such as:
1. Cultural differences
Outsourcing can involve working with suppliers from different countries or regions with different cultures, values, norms, and practices. This can create misunderstandings, conflicts, and inefficiencies if not appropriately managed.
2. Quality control issues
This can involve losing some control over the quality of the products, especially if the supplier does not have adequate quality assurance systems or standards. This can result in defective or substandard products, which can damage the reputation and customer satisfaction of the business.
3. Cost implications
This involves additional costs, such as transportation, customs, tariffs, taxes, and insurance, which can offset the savings from lower labour or material costs.
Therefore, businesses should balance the benefits and costs of reducing lead time and consider the trade-offs and alternatives.
For example, businesses can outsource only some parts or stages of the production process or use a mix of local and global suppliers to optimise the lead time and cost.
Businesses should also implement risk mitigation strategies, such as diversifying the supplier base, conducting regular audits and inspections, and having contingency plans to cope with disruptions or uncertainties.
Stay Ahead of the Competition with Faster Lead Times in Outsourced Manufacturing
Outsourced manufacturing services constantly evolve, and lead time reduction is at the forefront of industry competitiveness. By implementing the strategies outlined in this article, businesses can gain a significant advantage in the race to deliver products faster and more efficiently.
If you’re looking for a reliable partner in outsourced manufacturing services to help you achieve faster lead times and stay competitive in your industry, then you can consider choosing Oakter and let us help you meet your production goals while keeping lead times in check. We are an advanced Indian ODM with wide-ranging expertise, shipping 500k+ products every month.