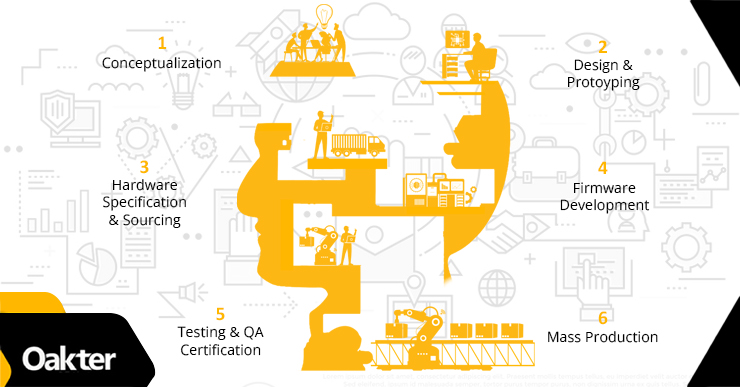
A Case Study on Turnkey Manufacturing Done Right: Factors for Implementation
Turnkey manufacturing has been gaining popularity in recent years as businesses constantly look for ways to streamline their manufacturing processes and reduce their overall costs.
However, implementing a turnkey manufacturing project is easier said than done- there are a number of critical factors that must be carefully monitored, managed, and executed for the project to succeed.
In this blog post, we will explore a case of turnkey manufacturing done right and look at some of the key factors that contributed to the roaring success of this project.
Electric PE and Oakter: Optimising a Partnership in Turnkey Manufacturing
This is the tale of two companies whose well-balanced collaboration has enabled them to complement each other and maximise their partnership by focusing on their core strengths.
On the one hand, there is ElectricPe, a software company contributing to the EV ecosystem by enabling billions of Indians to quickly locate an EV charging station near them and check its availability in real time instead of waiting in long queues or driving miles in search of one. They collaborate with thousands of independent charge point operators that provide services to EV users.
As Electric PE witnessed a rapid demand for its software, as a logical next step to grow its company and brand, it decided to diversify into EV hardware, namely charging points. However, hardware manufacturing was not its strong suit, but this could not hinder its growth plans. Hence, it sought a solution through a strategic partnership.
Oakter, on the other hand, is an advanced Indian ODM company that manufactures cutting-edge electronic hardware for various industries. It designs, develops, and manufactures high-quality IoT products.
In fact, Oakter is among the 27 companies approved by the government for the PLI 2.0 scheme for domestic IT hardware production.
Electric PE decided to leverage a turnkey manufacturing approach and partner with the reputable Oakter to produce high-quality chargers, giving them an edge in the market.
Factors Behind the Success of Collaboration
Let us explore what factors contributed to this successful partnership in turnkey manufacturing.
1. Planning
The first step to this successful project was careful planning. Electric PE and Oakter worked closely in the initial stages to strategise the project. To achieve this, they:
- Planned and identified the key requirements to produce EV chargers
- Ensured that the project was properly scoped and resourced
- Conducted a comprehensive analysis of Oakter’s existing processes and manufacturing capabilities
This understanding enabled them to develop a clear action plan for producing the EV chargers, including timelines, milestones, and deliverables.
2. Communication and Collaboration
The success of this turnkey manufacturing project relied heavily on communication and collaboration between Oakter and Electric PE. This included the following measures:
- Established strong communication channels to discuss EV charger specifications and design requirements.
- Remained in close contact throughout the implementation process and held regular meetings to review the project’s progress.
- Identified issues/ risks and addressed them early on- before they became major problems.
This transparent communication also helped to build trust and confidence between the two parties, which was crucial given the long-term nature of the relationship.
Overall, through open communication and alignment of their goals and expectations, they ensured that the result was an EV charger that exceeded the client’s vision and expectations.
3. Flexibility in Design and Customization
One of the benefits of turnkey manufacturing is that it offers companies the advantage of customised product development. Oakter and Electric PE could align their EV charger design to suit the market’s requirements.
- Oakter provided Electric PE flexibility of design and accommodated changes and iterations as and when required.
- Tailoring the manufacturing to specific customer requirements facilitated the creation of competitive and hi-tech EV chargers.
As with any complex project, some unexpected challenges and issues arose during implementation. However, the companies’ willingness to adapt, iterate, and make the necessary changes to the original plan enabled them to stay on track and ensure that production continued without any issues.
4. Quality Assurance and Compliance
Oakter and Electric PE were focused on maintaining high-quality standards. For this, they:
- Committed to ensuring stringent quality checks of the EV chargers throughout the production process.
- Conducted rigorous inspections of raw materials, electronic components, and finished chargers to identify any deviations from specifications.
- Focussed on maintaining and adhering to safety requirements and regulatory standards.
- Closely monitored certifications and compliance requirements.
This emphasis on quality helped Electric PE deliver reliable and safe products to its customers, gaining their trust and loyalty and maintaining its reputation as a reliable and high-quality brand.
5. Performance Monitoring and Continuous Improvement
Electric PE and Oakter monitored and evaluated project performance regularly to ensure ongoing success. They also:
- Identified potential bottlenecks, inefficiencies, or areas for improvement.
- Took prompt corrective action and enhanced their processes to maximise their outcomes.
Through a continuous focus on improvement, Electric PE and Oakter were able to enhance the efficiency of their manufacturing process and stay ahead of the market competition.
6. Establishing a long-term relationship
One key factor contributing to the success of the Electric PE and Oakter partnership was their commitment to a long-term relationship.
- Electric PE recognised that the turnkey solution was not just a one-off project but rather a long-term partnership with Oakter.
- They were willing to invest in the relationship and work closely with the Oakter to identify new opportunities and areas for improvement.
This commitment to a long-term relationship also helped to establish trust and confidence between the two parties. It ensured that their partnership would continue to be effective and efficient in the long run.
Final Note
This case study of Electric PE and Oakter provides valuable insights into the key factors contributing to the success of turnkey manufacturing projects. Careful planning, effective communication, a focus on quality, a willingness to adapt and change, and a commitment to a long-term relationship are all important factors that helped them ensure that the turnkey solution was implemented successfully and exceptional results were achieved.
Hence, this case study serves as a testament to the immense value of turnkey manufacturing, which, when done right, can provide tremendous opportunities for growth, efficiency, and profitability by allowing companies to focus on their core competencies, streamline their operations, and reduce costs without sacrificing quality or reliability of their products.
To partner with us on turnkey manufacturing, get in touch.